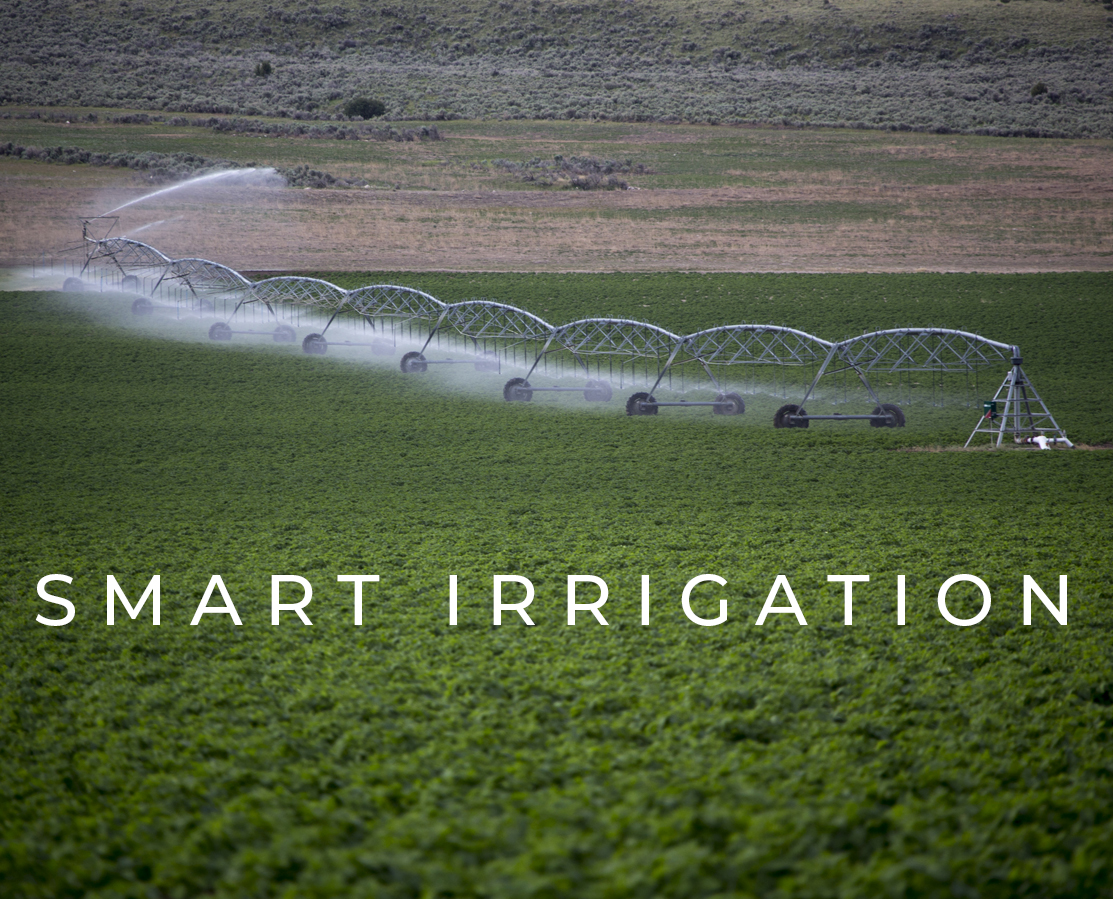
Tangible Results of Smart Irrigaiton
Each July, field inputs come together for the anticipated fall harvest. Successful growers know the importance of irrigation uniformity in maximizing these inputs for yield and grade. At the same time, rising energy costs are a continuing challenge. A critical need exists to continually monitor growers’ irrigation systems to ensure those returns year after year.
Agriculture has a tremendous history of rapidly adopting new technologies that provide returns on investment. We hear a lot today about new tools that provide artificial intelligence (AI) for our mechanized irrigation. Variable rate irrigation (VRI) is a tool being tried in many areas. These technologies definitely have a place in the modern irrigation world, but it’s important to remember the basics too, namely, identifying and replacing wornout equipment and ensuring systems are operated properly.
Several years ago, Brad King, Jeffrey Stark and Dennis Kincaid published a bulletin with the University of Idaho called “Irrigation Uniformity.” They evaluated 45 commercial fields under sprinkler irrigation systems in southern Idaho in 1995. The highlight, then and now, is the importance of maintaining high uniformity of a sprinkler system. By simply upgrading the sprinkler system from 70 percent CU (Christianson Uniformity Coefficient (the most common quantitative measure of irrigation uniformity) to 90 percent provided a return of $144 per acre in 1995.
Irrigation sprinkler packages of today are even more efficient and uniform, and in many cases are being used at lower pressure, are easier to maintain, and include options to reduce the plugging that is often seen in surface water conditions. Local irrigation dealers’ sales, service and parts teams can help growers procure and maintain the right irrigation package for their individual farms, soils, topography and management practices.
Utilize the tools available to get the highest uniformity along with the widest sprinkler wetted diameter to minimize application rates and limit runoff, and find a droplet that matches your specific soil and topography. Manufacturers offer a range of devices with very specific droplet characteristics. Over the past eight years, the USDA-ARS Research Station in Kimberly, Idaho, has done extensive work on surface sealing and runoff concerns for a range of soil classifications across Idaho that can be related to soils across the world.
For many years, the Columbia Basin has had the benefit of frequent aerial imagery that allowed up-to-date photos of the field to spot problems including plugged sprinklers or patterns in the field. The technology is available almost everywhere now and brings frequent satellite data to provide these near-real-time observations. Recent announcements within the industry indicate the potential to notify the grower via AI if an anomaly is detected with the field data.
This time of year, the real challenge can be just keeping everything running. With the monitoring and telemetry controls available, we have the ability to identify a problem on our cell phones instead of finding it the next morning when making the rounds to check the pivots. Everyone on your farm team needs to know how important uniformity is for optimum production. Everyone on your team can be part of the solution to maintaining high uniformity. When a sprinkler is damaged or missing, it is critical it is replaced with the correct nozzle and not just with what happens to be available in the pickup. Sprinklers, nozzles and pressure regulators wear out. Water quality, pressure and hours of operation are all factors in this.
It is important to monitor pressure at the pivot point and use this as a baseline for change. Check the pressure after the pivot has been running for a day or two, then measure at the same location in the field each time. Keeping track of the pressure year over year or even month to month helps spot problems. Too-low pressure will compromise the flow regulating devices, pattern and uniformity. Too-high pressure may indicate plugging and change in flow through the system.
In July it may be too late to update your sprinkler package and reach the best yield and grade, but if you have a problem and don’t address it, you could face even greater losses. When you observe a problem, the first thing to do is check for plugging. A small amount of organic material from surface water or cinders from the well can partially plug and reduce flow from the device. Always check for material on the inlet of the pressure regulator, the nozzle and the plate.
The second major problem is pressure. When all systems are operating, it may not be obvious that you are operating at lower than design pressure. Pressure regulators normally require an extra 5 PSI to allow proper flow exiting the nozzle. For example, the minimum design pressure for a 20 PSI regulator is 25 PSI. Optimum pressure must be considered in the design phase of the installation and needs to be monitored each year. A pressure gauge on the end of a system can ensure proper operating pressure is maintained throughout.
The third point is wear on the nozzle. Ten percent wear of the nozzle allows for a 20 percent flow increase at the same pressure. Finally, wear to the plate can change the pattern and affect throw distance and uniformity.
Another way to be smart about your irrigation is to check out new tools available for the end of the iron. Not only can you pick up additional coverage, you can provide a buffer around the edge of the crop to reduce heat sink issues and trash buildup in the overhang.
Many manufacturers offer options to easily clean nozzles, and even allow operators to shut off and backflush the nozzle. In areas where water and power management is critical, consider the option of having dual nozzles for the device that allow for a very quick change. Many growers can manage water availability by switching in-season to meet crop demands or water availability.
A final area to consider is the control valve at the pivot. All valves are not the same, and it is important to look at the friction loss through the valve. Local power companies can help growers calculate what each PSI costs an individual operation per year. A simple example below shows the cost of each PSI generated.
Contact your local dealer if you have a question. They will be glad to help and can provide answers to application concerns and relay the new innovations available. Take a few hours and attend a field day and visit a new machine to see what options are available. Visit with your neighbors, as they may have some of the same concerns. Saving water, energy, saving labor is our goal and should be yours.
Written by Don Zimmerman for the Potato Grower's July 2019 Issue